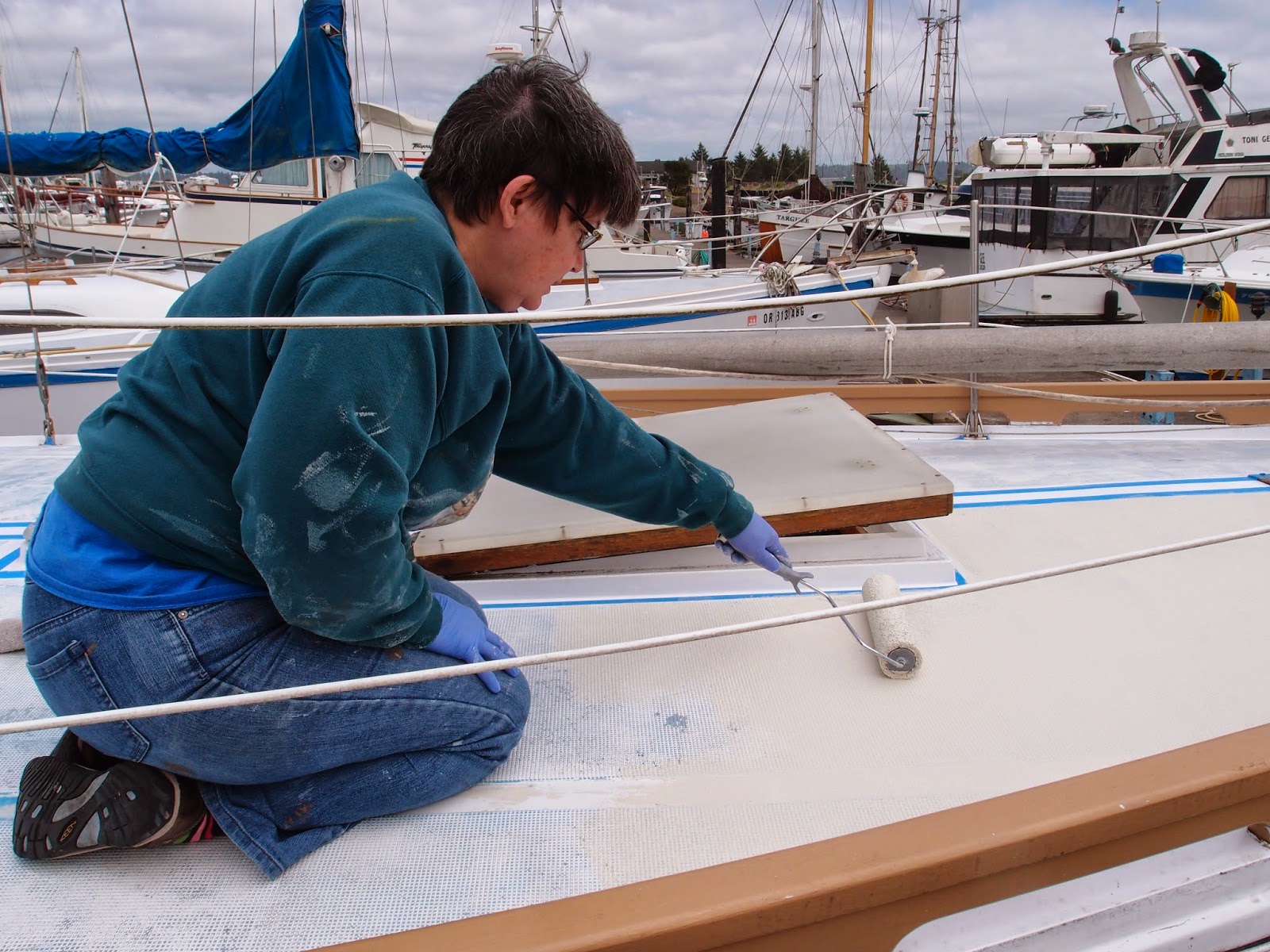 |
Weeks of hard prep work finally pays off as Virginia applies the first coat of our non-skid. |
Weeks of hard work on her knees last fall finally paid off when Virginia rolled on special non-skid paint on the deck of Oceanus last weekend. The decks look beautiful! To my eye they look even better than new.
When
Oceanus came out of the Columbia Yachts yard in Costa Mesa back in 1971 she had robin-egg blue non-skid areas with off-white water channels surrounding them. I'm sure they looked groovy just a couple years after The Summer of Love. Over the years the decks were pierced with vents and deck gear that now are long gone. They were beat up and painted two or three times, first with grey then with white paint. By the time we purchased the boat the decks were an ugly mess.
Worse still, all that paint filled in the texture of the molded in non-skid pattern making it unsafe. For two or three days each week for several weeks last fall Virginia was on her knees stripping off the old paint with
Citristrip and wire brushes and lots of elbow grease digging down to the original robin-egg blue, diamond-patterned non-skid. It was a lot of hard work: she came home beat. It was also a classic it-looks-worse-before-it-looks-better project. Way worse.
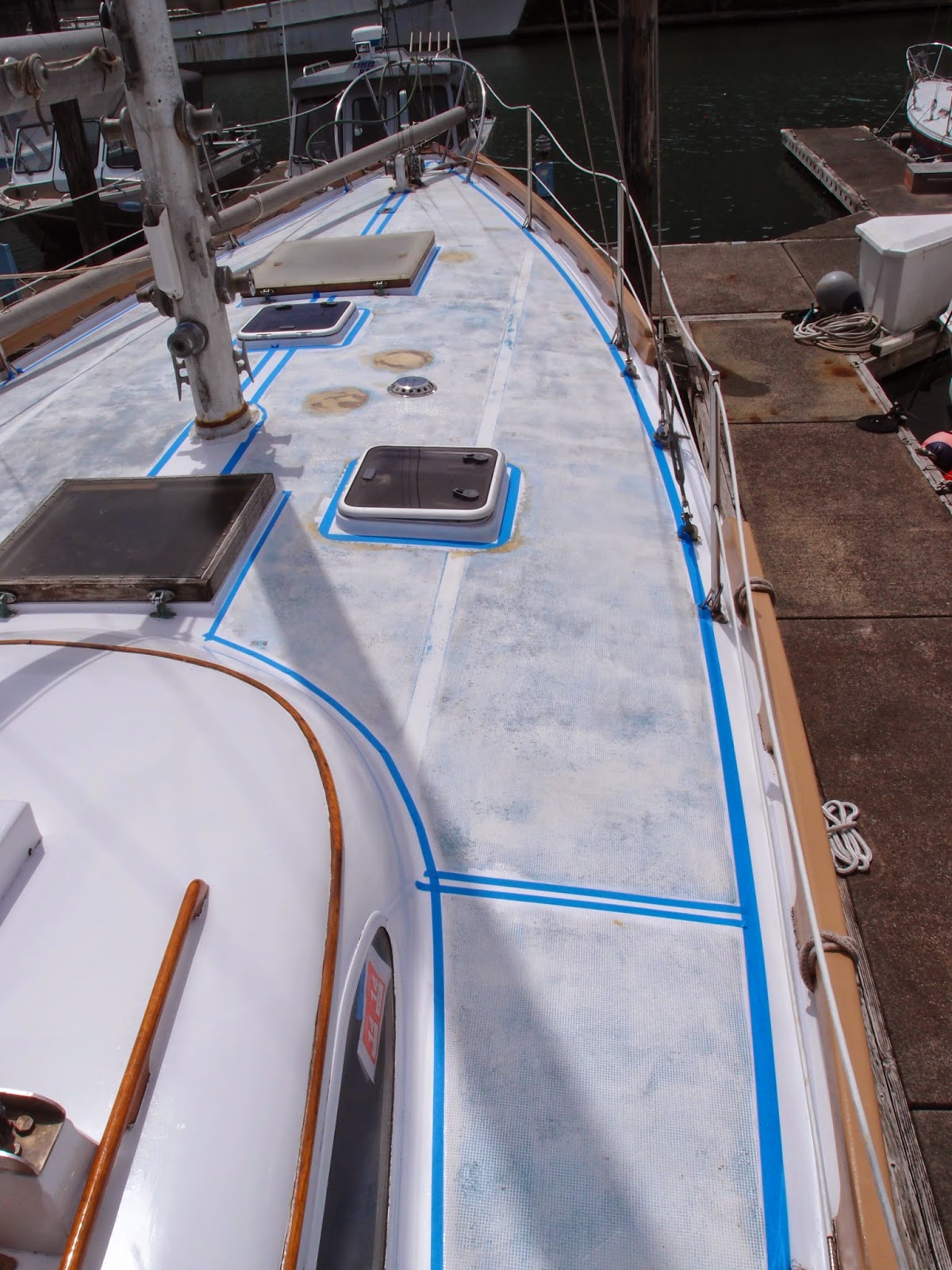 |
Oceanus's deck taped and ready for non-skid. |
When she finished the stripping and sanding, she painted two coats of white
Brightsides polyurethane paint in the water channels bordering the non-skid areas. Things started looking better. But just when she was ready for the big payoff -- painting the non-skid -- the Northwest rains descended. Since October there hasn't been the three days in a row of good weather she needed to apply the special non-skid paint. That changed a couple of weeks ago and things started looking better.
Before she started this project last year Virginia researched several non-skid paint options and finally decided to use a coating called
Ecoprocote Eco-Tuff Flex Formula Fine Aggregate in the wheat color. It's a low-VOC, high-traffic, rubberized non-skid industrial floor coating that has ground-up recycled tennis balls to make it grippy. The makers, Eco Safety Products, describe it as "The highest quality 100% Acrylic emulsion and Urethane dispersion with advanced bio-based technology that offers outstanding abrasion, hot tire pick-up, chemical, water, and weather resistance for interior or exterior use. It is a breathable self sealing, uniquely hard yet resilient rubberized non-skid coating that waterproofs, protects, and provides a non-aggressive barefoot friendly texture." I think it was the barefoot-friendly texture that sold us.
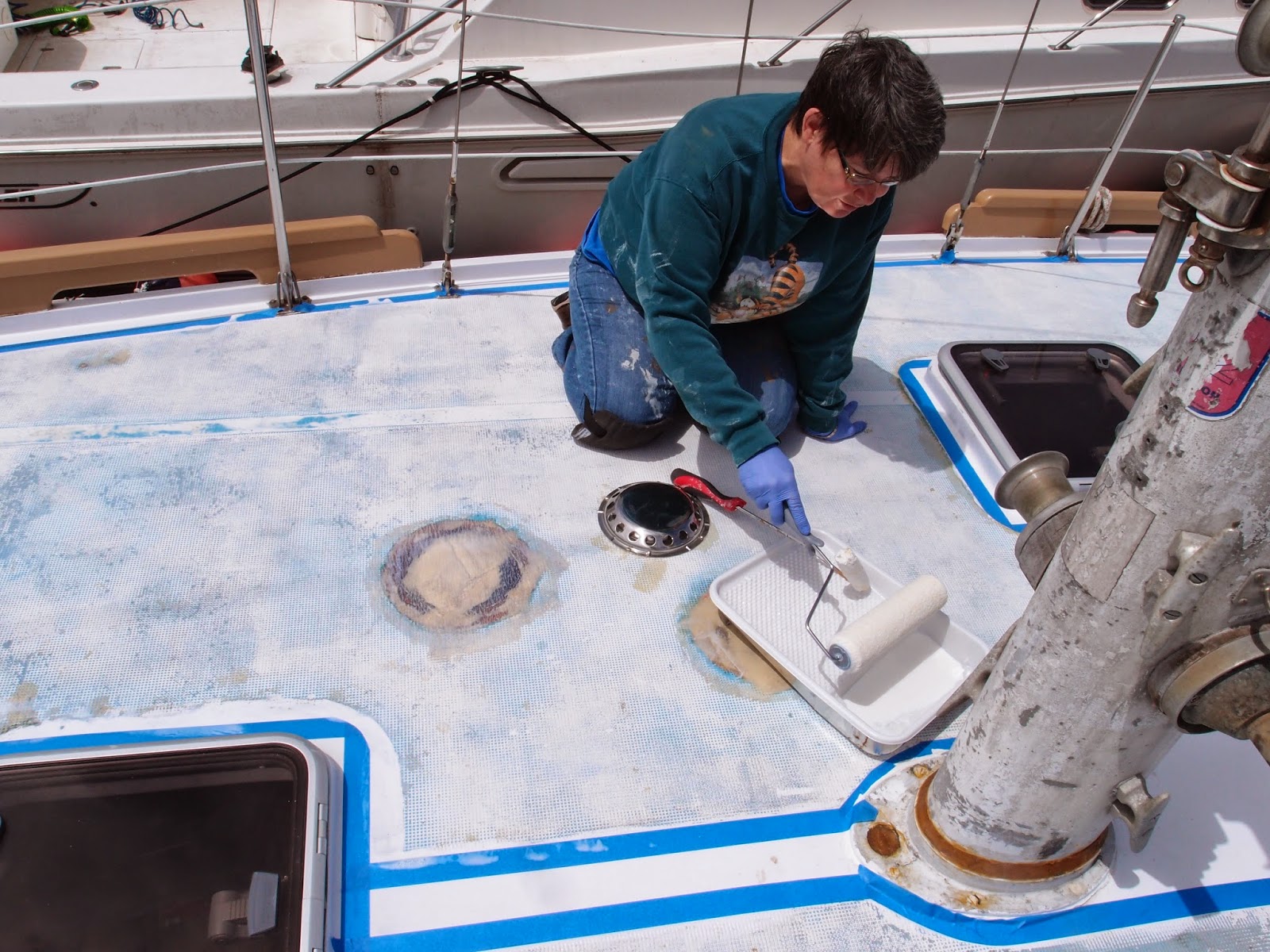 |
Virginia applies the special primer for the Eco-Tuff non-skid coating. |
The special primer for the Eco-Tuff looks like skimmed milk, goes on thin and drys tacky. Virginia had half a gallon left over when she finished coating all of the boat's non-skid areas. The non-skid coats must be applied within 48 hours of laying down the primer.
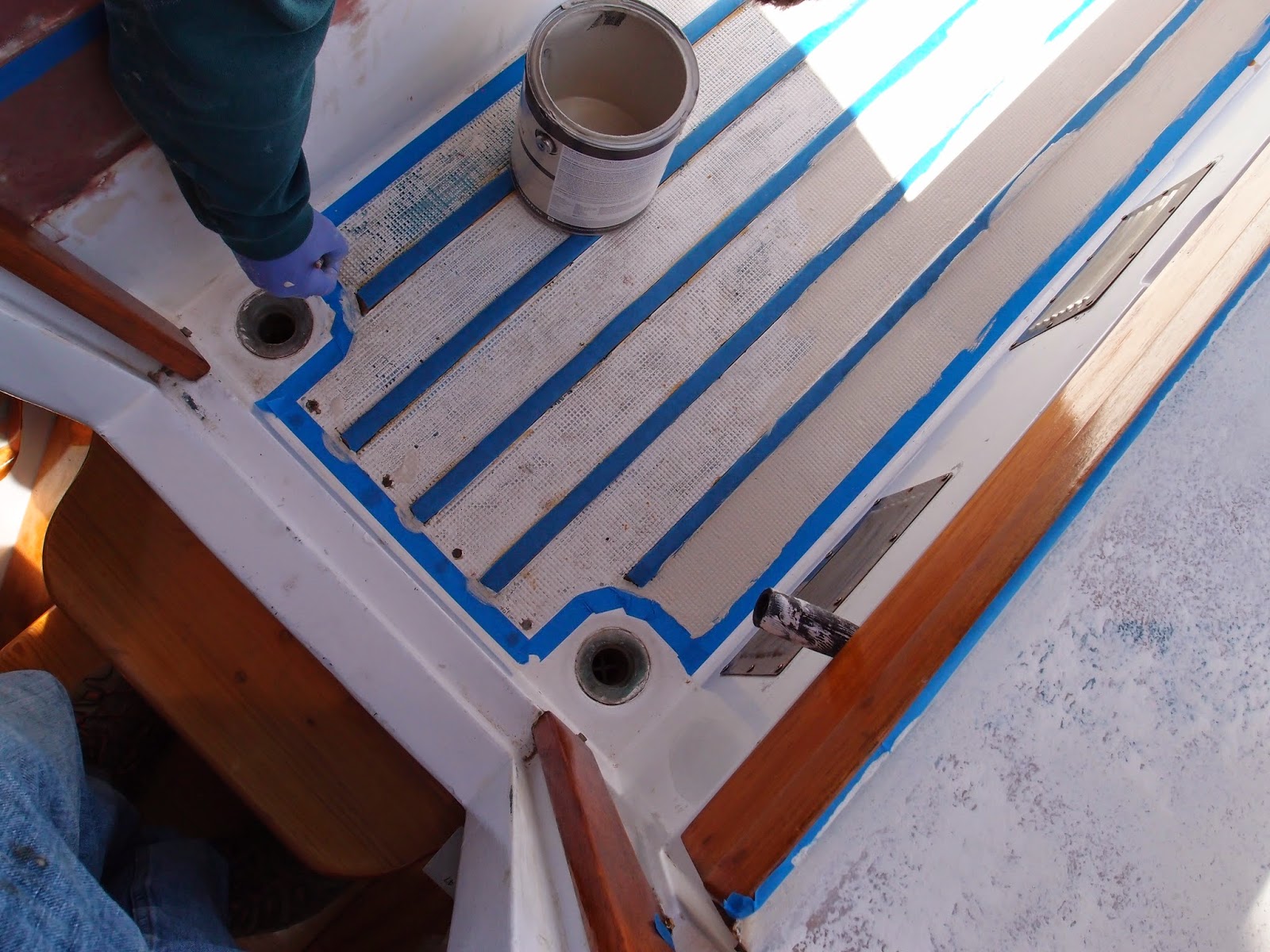 |
The cockpit get's its first coat of non-skid. The teak strips on the sole of the cockpit are taped off. |
The final coats are about the consistency of thinned oatmeal and must be stirred well every time before filling the paint tray. The stirring part is important to get a consistent look to the surface. To apply it you need a special roller cover you can buy from the Ecoprocoat folks. (The coating is water soluble so cleaning the roller between coats is not hard. We bought three roller covers just in case.) This stuff goes on thick so it doesn't go very far. Two gallons of the final coating covered two coats on the non-skid areas of the deck and in the cockpit. We ordered a third gallon so we can apply a third coat as recommended for high-traffic areas.
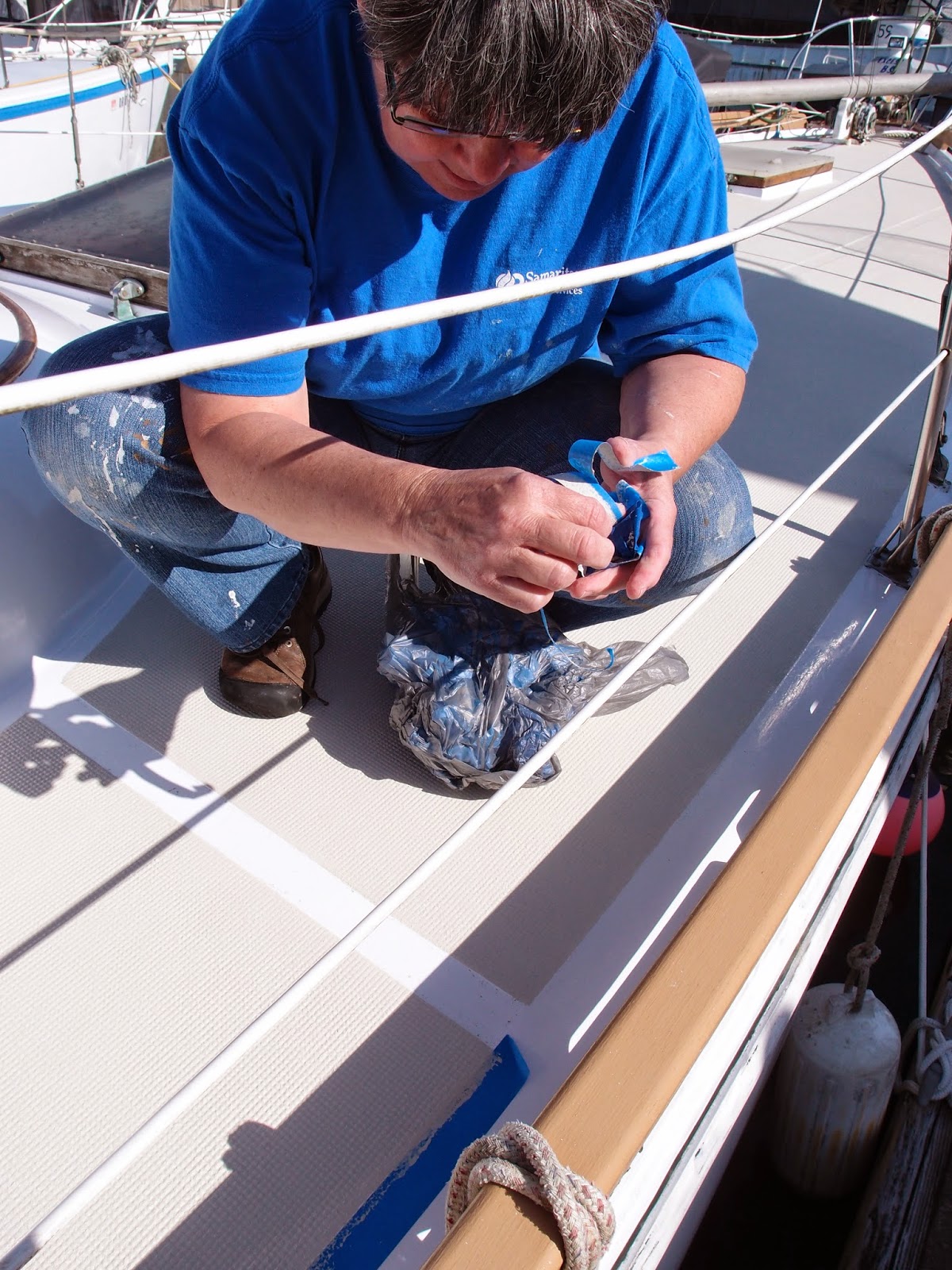 |
After two coats of non-skid Virginia removes the tape. |
We struggled with the color selection. We didn't want something too dark that would be hot in the tropics but we also wanted something that was easy on the eyes. The Wheat color turned out to be the right choice for us: not too dark and it looks good with the color of the canvas and bullworks. They didn't offer it in groovy robin-egg blue -- not that we would have picked that.
The best part about the new non-skid is way it feels. Your footing is secure both with bare feet and while wearing our Keens (the best shoes and sandals you can buy, in our opinion). In bare feet it feels soft and a little squishy, like the soft matts sometimes used in children's play areas or the running surface on a high-tech track. The Eco-Tuff folks also claim it has some insulative qualities, which won't hurt when the sun is beating down on
Oceanus's huge deck.
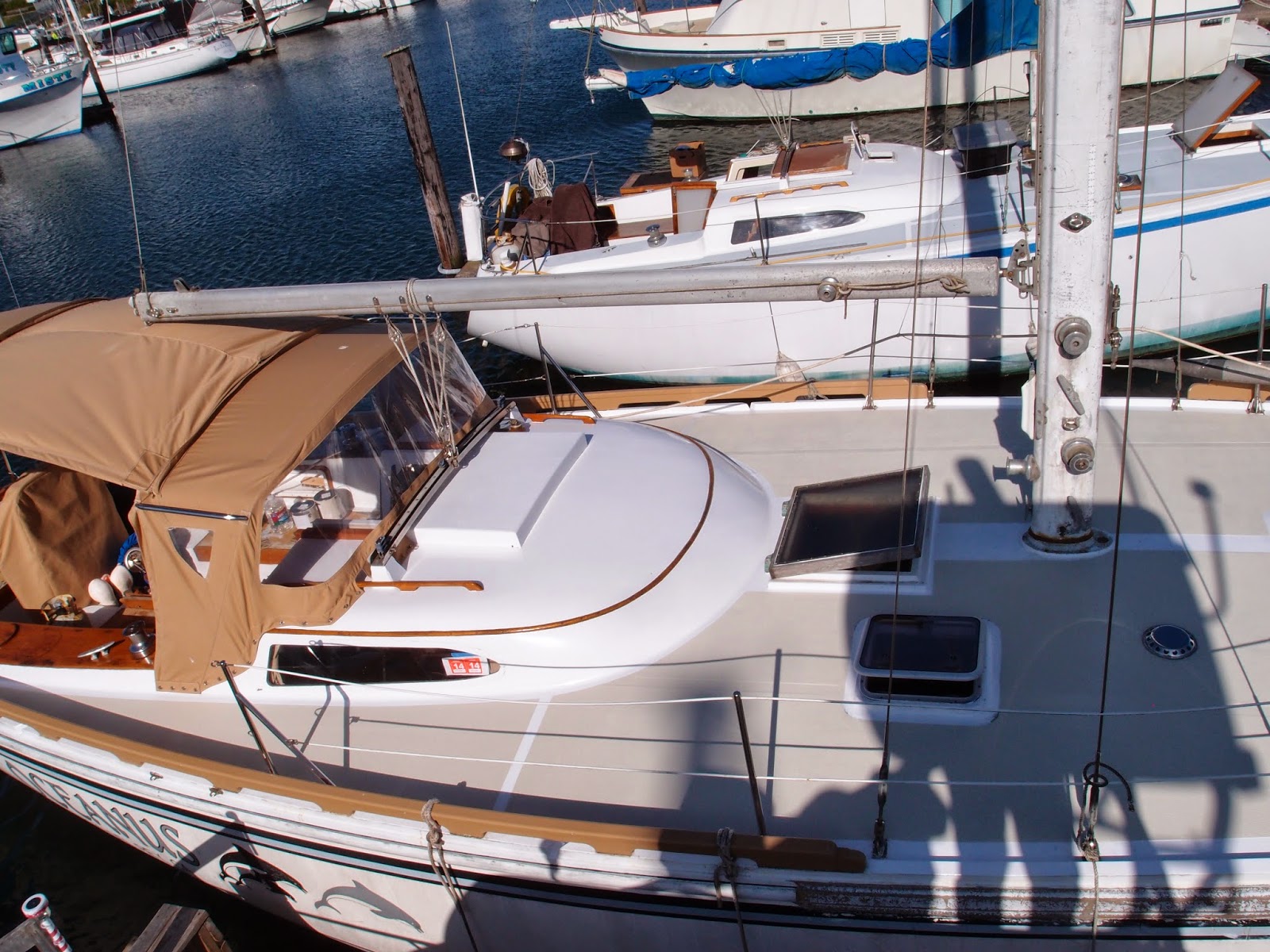 |
Beautiful decks at last! |
We couldn't be happier with how it looks and feels. Now we will wait to see how it holds up during actual use. Here's hoping Virginia's hard work pays off long term.